
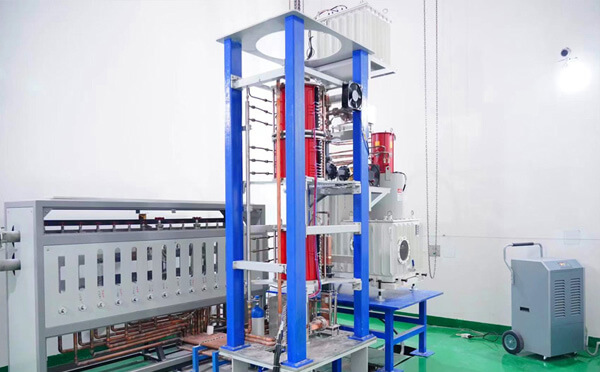
Accelerator control cabinet
The control and safety protection system of the accelerator is composed of a programmable controller (PLC) and a master computer, which can control all kinds of logic program control of the accelerator, such as system preparation, electron beam irradiation, cessation of electron beam irradiation and shutdown.The system can monitor the accelerator and set the parameters, and has the function of safety interlock protection. When the abnormal situation occurs, the control system can automatically cut off the high voltage system of the accelerator and display the fault state.Schematic diagram of control system
The control system consists of 1 main control computers and 4 PLC.The schematic diagram of the control system is shown in the figure above.The PLC used in the system is the S7 200smart series of SIMENS.PLC's CPU is connected through the MPI bus.PLC and distributed I/O are connected by PROFIBUS bus.Rs485/232 bus is used to connect PLC and terminals such as frequency converter, temperature controller and ion pump power supply.The main PLC and the monitoring computer are connected by Ethernet, and TCP/IP protocol is adopted to realize network control by remote monitoring and maintenance system on the Internet.The software is written by STEP 7 and C language. Some hardware functions are implemented by software, making the whole system easier to test, manufacture and maintain.
Functions implemented:
1. Realized the monitoring and control function of various input and output quantities, controlled the accelerator according to reliable control logic, and ensured the safe and stable operation of the accelerator.2. Two control modes can be realized: manual control mode and computer control mode. Manual mode includes debug mode and normal operation mode.
3. In computer control mode, there are also operating mode (for upper computer), monitoring mode (for remote monitoring) and debugging mode (for installing and debugging subsystems).Under the mode of operation, can also according to the actual requirements change many parameters, mainly including: repetition frequency, the range of temperature and the temperature of the water cooling system, vacuum protection threshold, speed of conveyor , etc.
4. In the computer control mode, the control program and database are integrated. Importing historical data directly into the database for query, it is helpful for monitoring and maintenance.The written independent software can read the data, and reappear the running process of the accelerator through the data. It can not only specify the time period of replay, but also the speed of the replay can be adjusted.After adding the function of the database, the performance requirement of the upper computer is improved.
5. Remote monitoring is realized through network.Under the premise of authorization, remote monitoring, maintenance and operation can be realized through the network (the operation control function is cancelled due to safety).The implementation of the network includes LAN (TCP/IP protocol), fixed telephone network and mobile communication network.The host computer can be used as a server, and it can be accessed by a remote computer through TCP/IP access control system.You can access the control system anywhere on the Internet.(this system is optional)